Hide Sortation & Tracking System
Sort and track your hides with ease
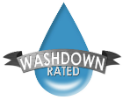
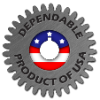
Major Components of a Hide Sorting & Tracking System:
- Hanging station
- Grading station input panel
- In-motion scale to weigh each hide on the fly
- SDS Controller to track chain movement and individual weighment data
- Chain movement distance encoding sensor
- Multiple drop station actuators
- Office production reporting permits real-time decisions
This hide sortation and tracking system allows processors to sort hides based on the weight, type, and branding marks. It gives plants the ability to sort green or cured hides to maximize efficiency.
Features & Benefits:
- Sort hides based on weight, branding marks, green or cured to maximize efficiency
- Overhead transport conveyor reduces injuries related to manually sorting each hide
- Sorting parameters and sorting performance can be sent to a computer network permitting upper management to view reports in real time
- Reportable information can include, but is not limited to, grand totals, tannery totals, raceway totals, weight range, and grade
- Significantly reduce sorting labor costs associated with grading, weighing, handling, tracking and dropping hides
Hide Sortation System Features:
How our Hide Sorting and Tracking System works:
The Vande Berg Scales hide sortation and tracking system typically controls the grading, weighing, and automatic sorting of the hides based on brand, weight, damage, drum accumulated weight, raceway accumulated weight, total count and total weight sort parameters. The chain transports the hide to the grader personnel, who inspect the hide for brands and damage. The grader keys the hide grade into a customizable designed grading panel. From this point, the hide movement is tracked by use of the distance encoding equipment.
The hide is then passed over an in-motion scale for weight determination. The hide is then transported further and automatically kicked off the conveyor system at the appropriate location.
Weight accumulations at each drop location are calculated to a specific target weight for effective tanning or inventory needs. Once drops reach their target weight, a beacon light can alert a forklift operator to replace the tub. Hides that don’t meet parameters continue on the conveyor to a catch-all location.
Reducing Tanning Chemicals Using Hide Sortation
Many operations that slaughter animals also harvest their hides to be tanned for leather in apparel, car upholstery, furniture, etc. Before hides can be used in other industries, they must be treated with chemicals. Hides present themselves in many different variations. If they aren’t sorted properly, processors can ruin hides by over-treating with chemical.
For this reason, a good sorting system ensures the to-be-treated hides will receive the right amount of chemicals.
One of the first steps after an animal has been skinned and the hide has been washed is a green grade station. Here, an employee performs a physical inspection to check the hide for holes and tears while also identifying the type of hide based off of the brand.
The three typical types are:
Native: This particular type of cattle has no brand and is the most valuable. A brand on the hide causes that portion of it to be unusable, so this hide is best used for larger products.
Butt: Next most valuable; any beef animal that has a brand within 18 inches of the hind end. This hide can still mostly be used but the lower portion cannot. Leaves roughly 2/3 of the hide although misses out on the toughest portion of leather from the rear.
Colorado (“Collie”): The least valuable portion; any animal not covered by the other categories. Becomes much harder and less profitable to use because the leather is smaller and of lesser quality.
The hide grader can be set up with a touchscreen or simple button interface to input the appropriate info.
After leaving the station, the hides go to scales and then are deposited into an appropriate location based off of the weight range and type of that hide. Our software can take this data and form trends, for example, to tell you what types of hides are coming in and how closely they fit ideal weight parameters.
The sorting drops each category into separate bins which are then dumped into vats of tanning chemicals to be treated.
Over-treating can cost a lot of money and ruin thinner hides so it is important to split the hides up into the right categories, so the process can be tailored to fit each one.
If chemical costs are too high in your hide operation, we can set you up with grading and sorting systems to give you the level of control that you need to optimize the operation.