Automatic Sortation Systems
Significantly reduce your sorting labor costs
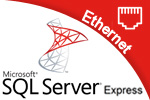
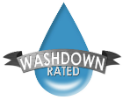
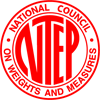
Industrial Applications
- Pork Plants
- Seafood Plants
- Beef Plants
- Chicken Facilities
No crazy high parts pricing – VBS uses standard, industry-available components that are easily attainable from multiple vendors, in the design and construction of our equipment assuring our customer economical, simplified, fast and efficient maintainability.
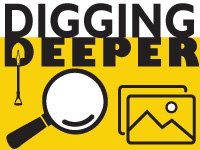
Additional construction details of:
Ham Sortation System
Pork Tenders Sortation System
Belly Classier Sortation System
Pork Loin Classifer System
Our automated Sortation Systems can significantly reduce labor and improve sortation accuracy and efficiency. Sanitary design makes for easy washdown. We can customize a classifier to your exact physical specifications and needs.
Features & Benefits:
- Significantly minimizes errors vs. doing manual sorting
- Reduces sorting labor costs and frees up personnel to do other tasks
- System construction such as stainless steel or aluminum is based on industry construction requirements/standards
- NTEP Approved conveyor scale ensures accurate in-motion weighing for weight-sorting applications
- Often used for automatically sorting food product such as pork primals, beef steaks, dairy, chicken, cheese, etc.
Sortation System Features:
FAQ
Rapidly sort product based on weight, grade, product type, visual characteristics (with camera), count, accumulated totals, barcode data into multiple bins, pack-off stations, conveyor lines/locations.
Sudden fluctuations in electrical power can cause considerable problems with sortation system timing. Also, if the sortation system is paused (or stopped), the entire belt must be cleared before it is started. VBS distance-based sorting systems do not have this problem.
If the network goes down, our controller will continue to store production records. When the network is restored, those saved records are available for upload. The main differences between our two types of controllers are primarily in the type of database, the user interface, and the amount of information that can be stored.
Primary Components of Sortation/Classifying Systems
- Infeed Conveyor to promote consistent spacing for the weighing process and/or allow manipulation by operators
- Conveyor Scale to weigh product for sort parameter determination
- Sorting Conveyor to transport product to classification bins and divert locations
- Diverts to sort product by mechanical means (i.e. pull/push/drop/tip/plow/air blow/shoe-sort, etc.)
- Bins to collect product for eventual trimming, further processing, boxing, bag filling, etc.
- Optional trimming scale work stations for further processing of product before boxing, bagging, case filling, etc.
Our Sorter Can:
- Sort by distance-based encoding to assure divert accuracy vs. problematic timer-based classifying systems
- Change the divert configuration while the system is sorting to allow maximum production flexibility
- Show product totals by grade, count, weight and product type
- Generate reports of current and total divert counts – allowing display with current and total divert accumulations
- View digital inputs, communication inputs, input buffers, divert buffers, group values and divert status during operation for diagnostics
Proper Product Handling When Using Automated Sorting Systems
When designing a sortation and classifying system, it is important to keep the fragility and stability of your product in mind at all times.
Products (such as apples, or egg cartons) can be damaged if a sortation system isn’t designed with the right features to match them. Rough handling of product is one of the biggest downfalls for a poorly designed system, but it is also rather difficult to eliminate entirely because of the system’s machine-like nature.
A sorting system requires that you have very precise and smooth divert action. If you can’t have too much power driving the divert, it will damage the product.
Our decades of experience ensures that the air output driving the divert is appropriately calibrated so divert impact is minimized.
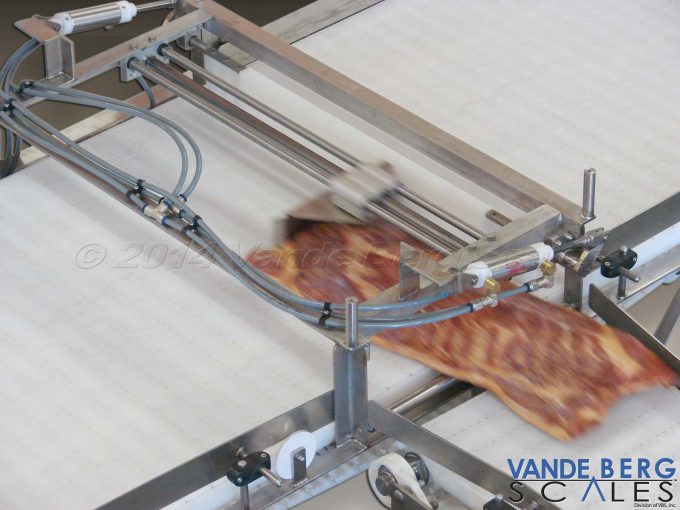
Some products are stubborn and like to stick to things like conveyor belts. These sometimes require a little extra “elbow grease” when being sorted.
In one case where we were dealing with a sticky product, we adapted the sorting conveyor so that it was at an angle. The scale itself stayed horizontal, but the conveyor itself was mounted at a small angle (10-20 degrees) so that gravity could assist the divert in guiding product off of the belt.
This allows the product to roll off the conveyor so it isn’t resisting the divert or getting stuck between the divert and conveyor.
Speaking of getting stuck, since there is a minuscule gap between the diverts and the conveyor, certain products can work themselves underneath pull-off diverts and get stuck, jamming up the system essentially.
To address this issue, we have installed a suspension that allows the divert to pivot upward allowing the wedged products to pass through. See image above.
If you need sorting or are having problems with a current sortation system contact us for sorting and classifying that you can trust.
Additional Sortation System Videos
2-Drop Sortation System for Pork Tenderloins
8-Drop Sortation System with Checkweighing Capabilities for Urethane Parts
6-Drop Ham Sortation System with Combo-full lights
Loin Sortation System with Liftable Conveyor Diverts
Rib Sortation with Pacing Conveyor and 6 Trim Stations
Want to generate reports and push product info to the floor?
Downloadable PDF Resources
Need a Quote in a Hurry?
Download our questionnaire and fill it out to get a quote.